Europlacer’s Stock Management Solution
Published: March 9, 2023
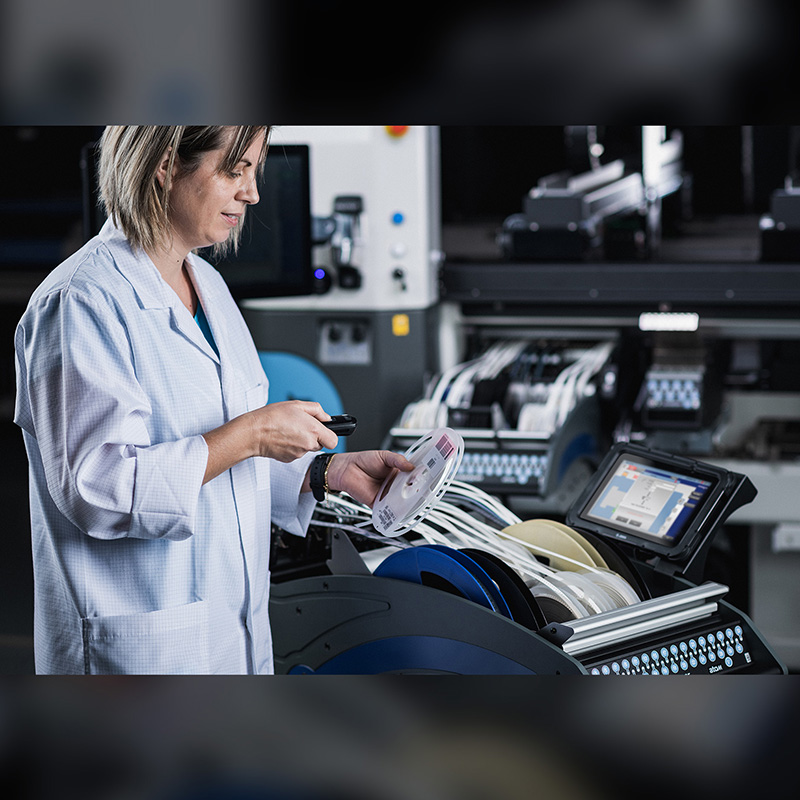
Production monitoring starts with component delivery with Europlacer’s Stock Management Solution.
Optimizing the production of your SMT line is essential, the Europlacer Stock Management solution can help give you complete control with real-time visibility of component stock levels and locations. Our solution will help you organize components’ procurement, save setup time for production and anticipate shortages on the line.
Component management becomes fully controlled when integrated with our online storage solutions or your own ERP system.
What’s the main benefit of the Europlacer Stock Management Solution?
On your SMT line, new reels entering the system will be identified by a unique code (UID) generated as a label by the storage tower or ERP. Our Stock Management solution becomes the central system that records, with fine detail, the operations concerning the reels. Information such as the consumption, location, association, and expiry date are detailed in the various production phases of the line. There is continuous communication between all systems such as the machines and storage towers which enables this real-time data.
The life of the MSL reel (Moisture Sensitivity Level) is monitored in the database as soon as it’s taken out of a humidity-controlled storage area and can be reset to zero after it has been in the oven. This means it’s not possible to program a reel if its expiry date has passed, which ensures all components used on a machine are relevant.
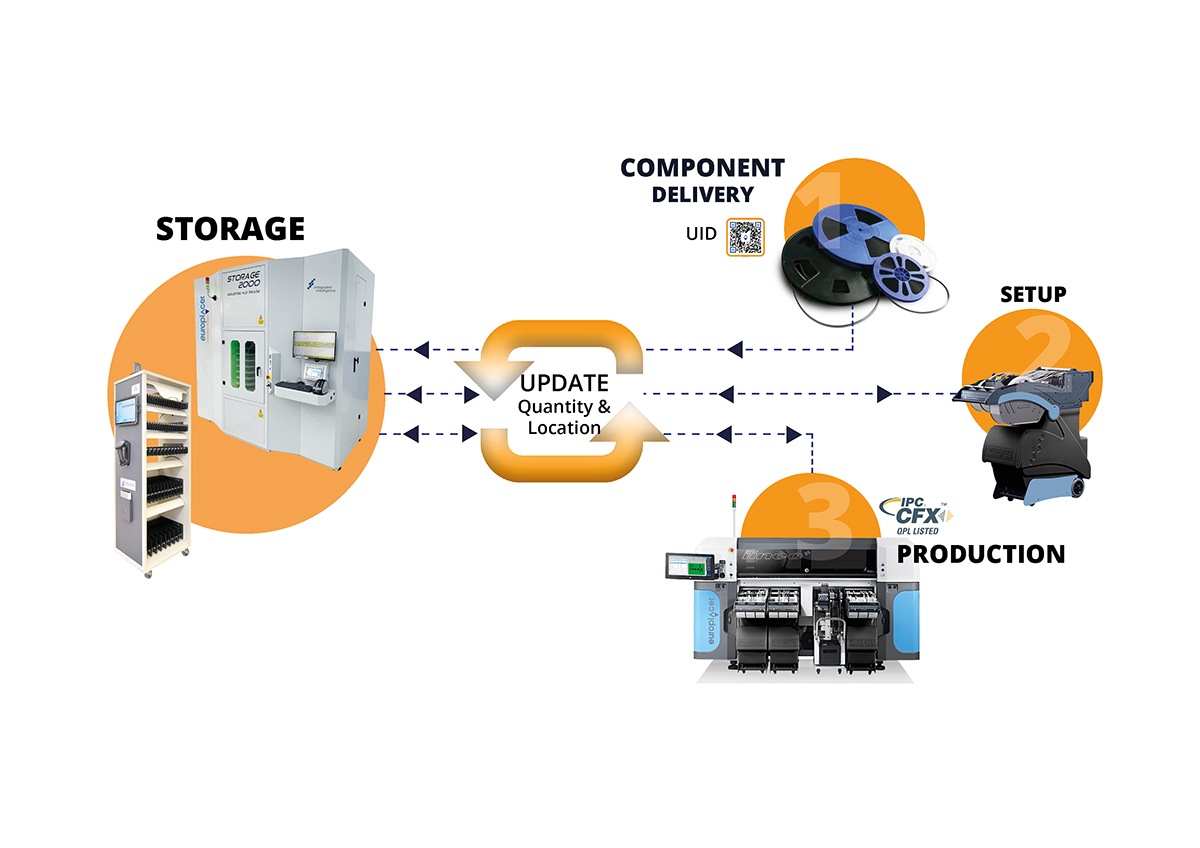
What value does this add to the set-up of production?
During production set-up, the ‘Pick List’ feature of our ii-Tab shows you what components you will need for future production. For each reel, the operator can check its remaining quantity as well as its location. The selection of the component reels can be done according to your criteria i.e started reel or the preferred location. It can also be identified if the selection concerns the whole production or only a section of it.
Once the ‘Pick List’ is selected, the operator can pick up the component reels from the locations displayed on the app. You can also send this list directly to the connected mobile racks.
"In the current context, Europlacer is convinced that the control of component flows in production is essential and must be simple. With our “Stock Management” option, we provide the foundation around which everything is best structured to support our customers towards this goal."
Nicolas Pogu, Europlacer R&D Director
How does the Stock Management Solution optimize production?
During production, our CSL app (Component Shortage List) makes it possible to monitor the progress of a batch. The app indicates the time remaining and knows which components will be out of stock within a configurable time period. This works with our ‘Pick List’ which can be used to generate a list of components needing to be replenished to avoid production downtime.
In the case of an unanticipated demand for components, a scan of the almost finished reel triggers immediate reel extraction from the tower or storage racks using the ‘Fast Extract’ function.
The Europlacer Stock Management Solution will enable you to have full visibility of your current status of stock plus smart features to anticipate component shortages for advanced planning. Your SMT line can be run at full efficiency with the help of our optimizing tools.