Europlacer presents its new range of iineo SMT placement machines.
Published: May 1, 2024
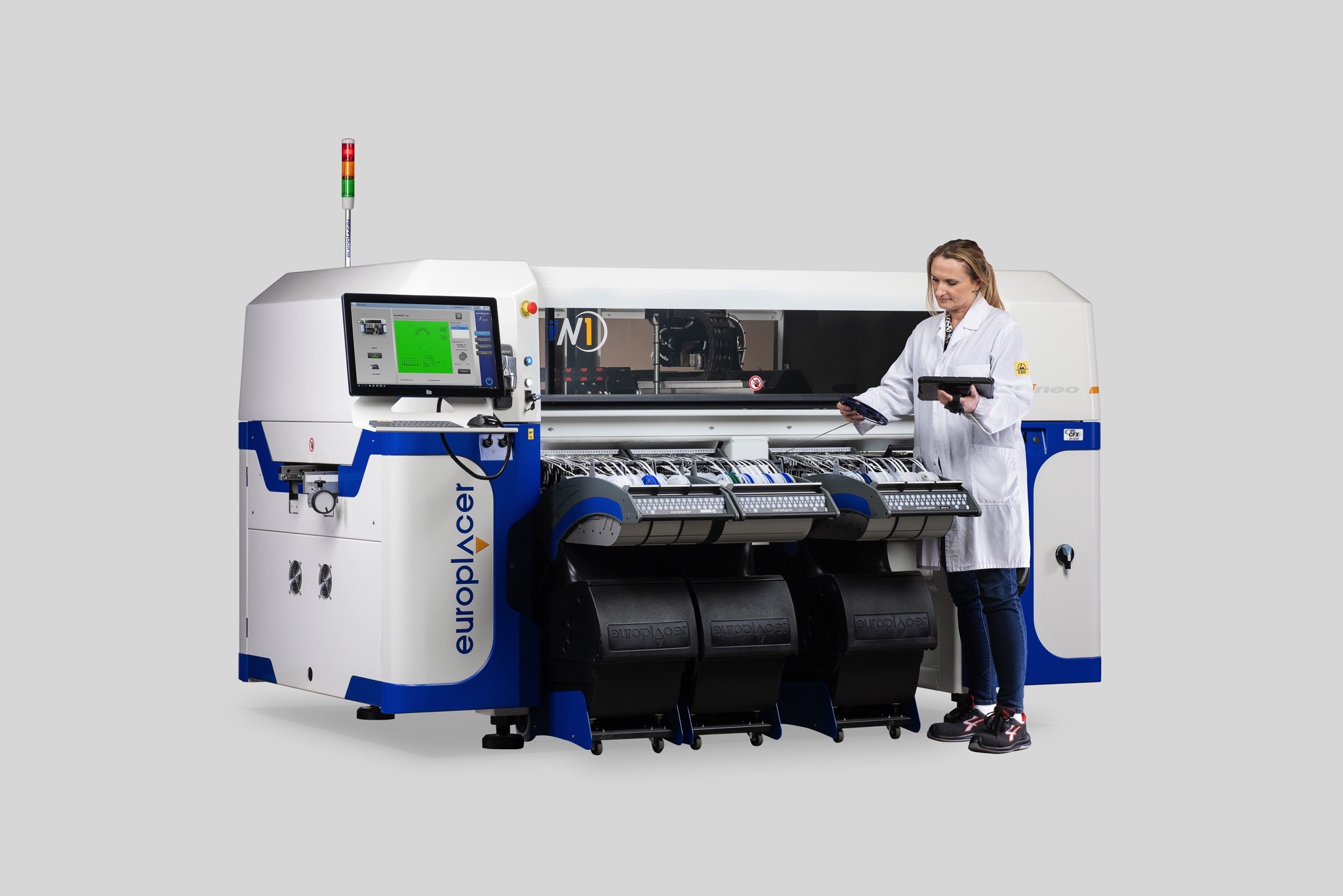
For more than 15 years, the Europlacer iineo placement machines have made their mark on the SMT industry with unique features and unrivalled flexibility. Today, Europlacer announces the launch of the second generation iineo pick and place machine.
The new iineo single-head and dual-head machines have been renamed ii-N1 and ii-N2. The hyper-flexible Tornado turret heads have been modernized and are still available with 8 or 12 nozzles.
While ii-N1 is the best in class for prototyping and short production runs, ii-N2 is the perfect compromise between speed and flexibility for high-mix production. The ii-N1 and ii-N2 can be operated at placement rates of 15,000 cph and 30,000 cph respectively.
While some of the features that have made the iineo a success have been retained, such as the very high on-machine reel capacity of 264 x 8 mm feeders plus 10 Jedec trays for ii-N1, a number of hardware and software improvements have been made.
One significant innovation is the intelligent conveyor. The boards no longer stop at a simple mechanical stop. Thanks to a set of infrared beams along the length of the conveyor, the PCBs can be halted in the most appropriate position to shorten the movements of the placement head, thereby optimizing throughput. Both machines also feature automatic motorized rail width adjustment as standard.
Machine performance is also supported by a redesigned machine vision system featuring very high-resolution ‘on-the-fly’ cameras, mounted both on the turret heads and on the machine frame as a fixed upward-facing camera for large components. Anticipating the miniaturization of components, the iineo range is capable of placing components ranging from 03015 metric to 99 mm x 99 mm in size and 34 mm in height with a weight of up to 300g.
For the twin-head ii-N2 machine, in the interests of productivity with PCBs that feature repeating patterns, only the camera on head 1 validates all the test patterns for each board, freeing up head 2 to only read the test patterns on the technical borders. This allows to save valuable production time.
Another key feature developed by Europlacer’s design department is Adaptive Auto Sequencing (AAS). As well as setting placement priorities to configure a sequence that maximizes productivity, AAS takes into account component footprints, nozzle profiles, PCB characteristics and turret head trajectory calculations to avoid collisions. The two new machines also deploy Europlacer’s proprietary 3DPS© technology, which adjusts the Z-axis displacement of each placement nozzle in real time to compensate for any deformation of the board, thereby limiting the need for anti-bending pins.
The new iineo generation is equipped with the latest ii-RC 5.17 operating software, which itself includes a host of new features, including an SQL database. This is strengthened by the integration of Siemens’ Valor software, fitted as standard on our remote programming stations.
Europlacer’s ii-Tab tablet not only becomes the operator’s mobile dashboard, but also replaces the micro-terminal as the feeder and reel programming tool. The ii-Tab brings together a number of functions, including the Pick List, which can now be used to reserve reels and automatically allocate them to a production order. Similarly, thanks to the Stock Management software, the list of components can be sent directly to the storage towers or mobile shelves at the line’s edge for automatic delivery of the reels. A total of 10 applications are available on the iiTab: a true ecosystem at the service of productivity.
As Europlacer is a key contributor to the IPC CFX standards, the ii-N1 and ii-N2 are of course CFX/IPC certified. This enables the collection of production data while facilitating connectivity between our machines and any other CFX/IPC-compatible equipment in a production line.
Integrated CFX, coupled with a tool for analysing the data collected, guarantees a greater understanding of production in order to better anticipate andmanage flows, materials and component stocks, and better understand the traceability of boards produced and components consumed.
This tracking also covers undesirable events that occur during production and are often invisible to operators.
Europlacer has designed its ecosystem around CFX because optimizing its industrial facilities requires both continuous observation of production performance data and the management of component stocks in connected cabinets and shelves, all linked to the factory’s ERP and/or MES.
With ii-N1 and ii-N2, Europlacer plans to open the doors to the industry of the future for its customers.
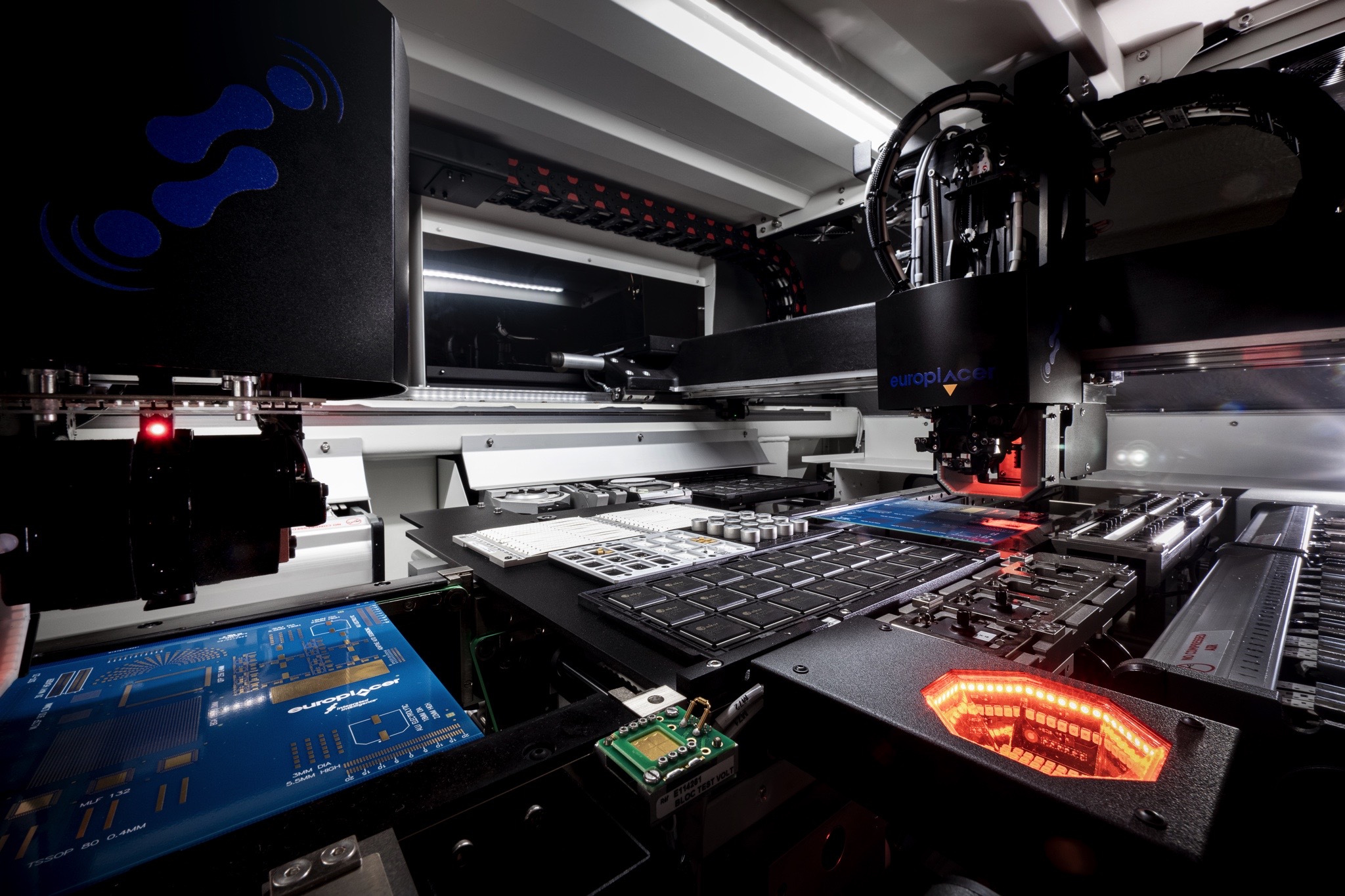
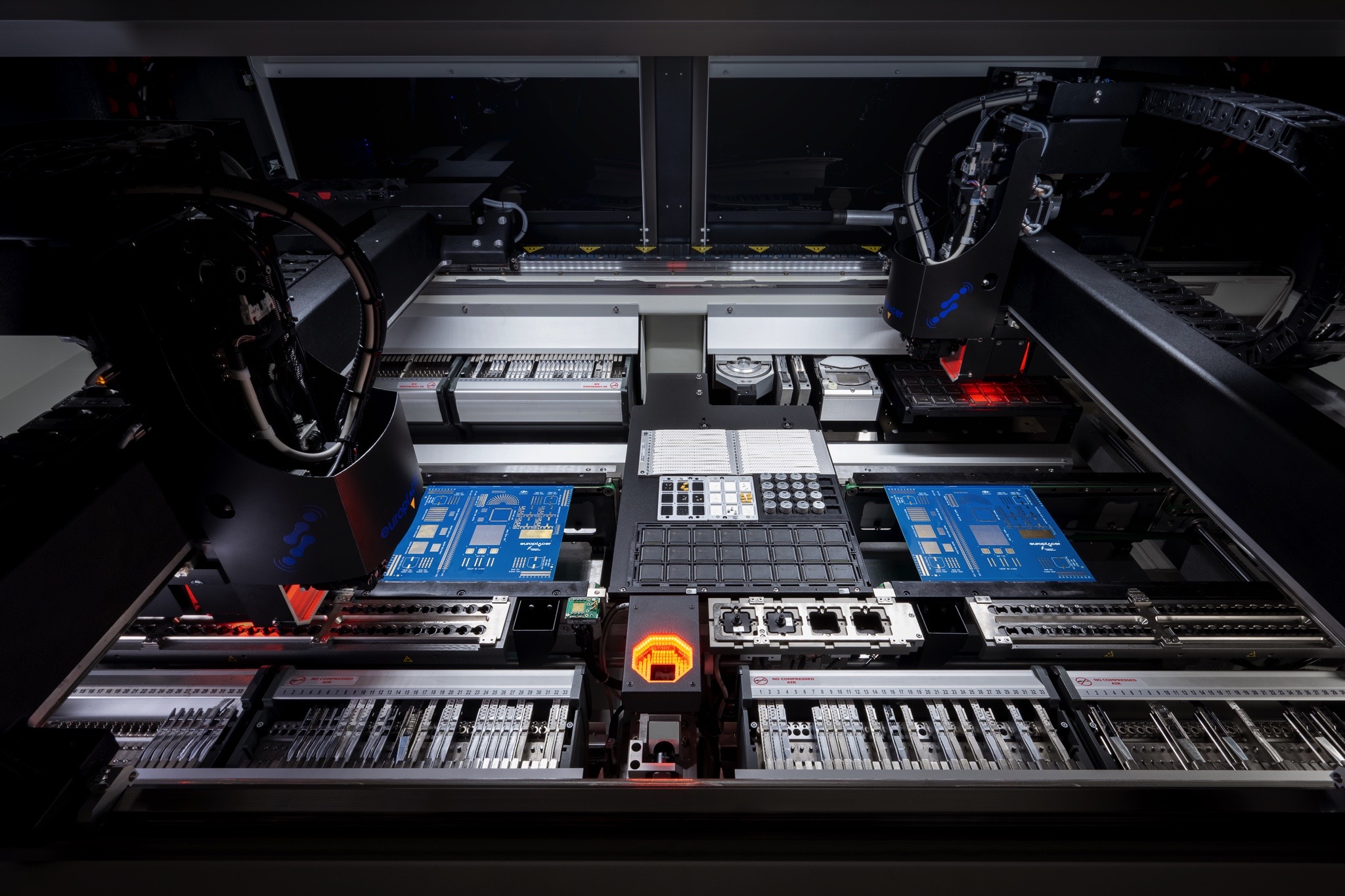