The various electronics industry standards and safety regulations impose specific test requirements and performance standards that components must meet. In addition, certain standards and industries (medical devices, aerospace…) have much higher reliability requirements than those applied to typical PCBs, and specific tests must be performed during PCB manufacturing to ensure component and board reliability.
Europlacer’s flagship placement platforms can test the electrical characteristics and polarity of components using an LCR Electrical Test bridge.
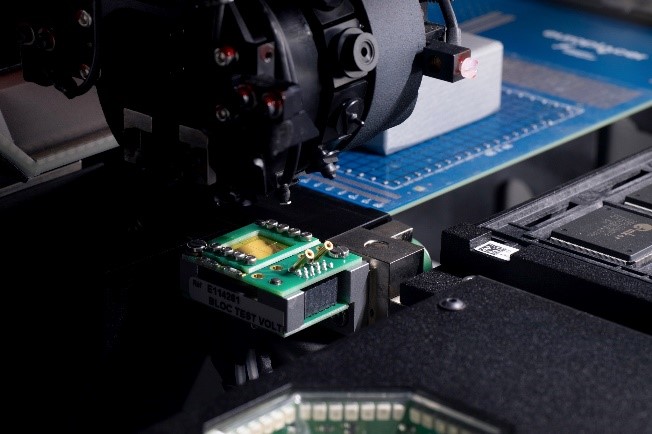
Description
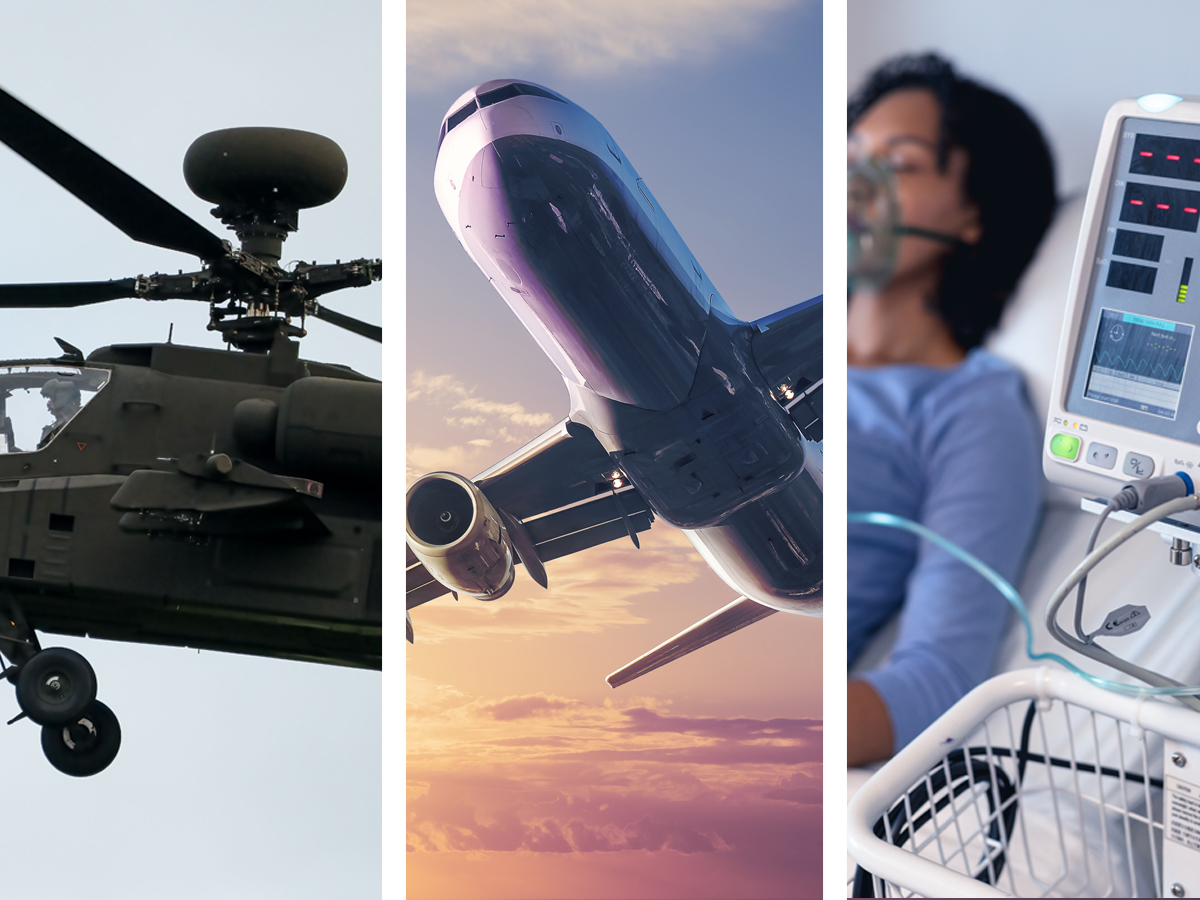
Defence, Aero, Medical
More than a simple test for presence, the tester measures electrical values using an LCR bridge. This ensures that incorrect value, out-of-specification or damaged components will not be placed during production. Crucially, the tester can be independently calibrated against all international standards & institutes. It guarantees you and your customer the statutory performance required when working on demanding applications.
The test pad is mounted securely inside the placement machine and does not compromise other platform resources. The test is performed during the placement process: after picking the component from the reel and before placing it on the board. Incorrect components are automatically rejected. Compared to other test solutions, Europlacer’s test pad method delivers better throughput and more accurate measurements of component value.
The tester can measure the characteristics of passive components (resistors, capacitors and inductors) and verify the polarity of diodes. Combined with Europlacer’s RC5.17 operating software, the test process will allow you to measure the characteristics of any type of diode with voltages up to 36V.
When paired with Europlacer’s traceability, you can record data on all passed tests and component rejections providing confidence that the test and placement process was completed within the required design and production limits.
Features / Benefits
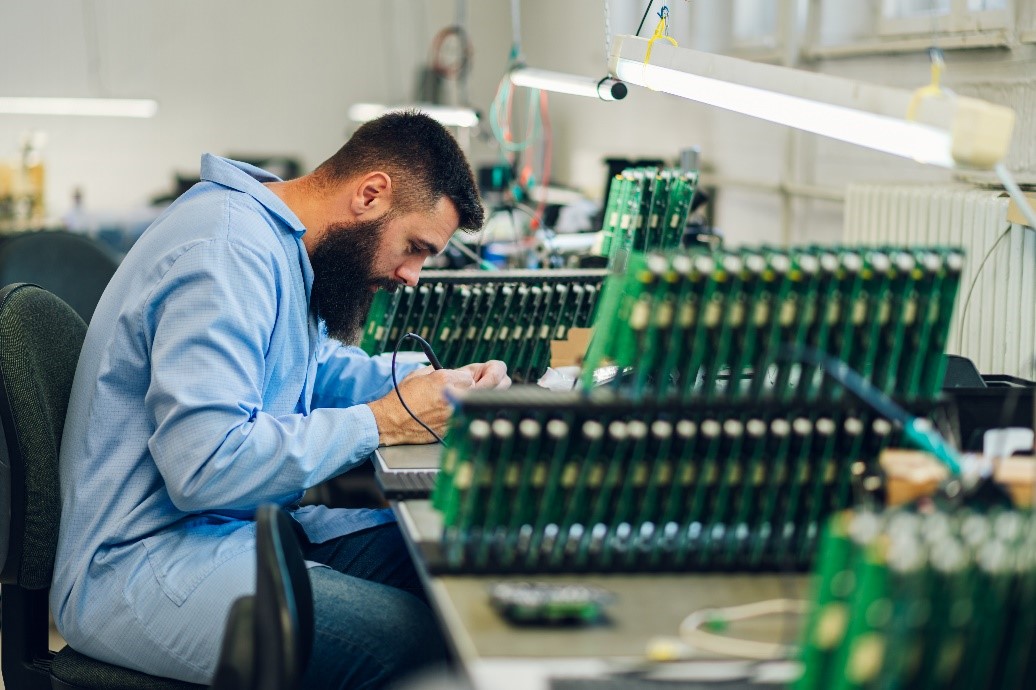
Guarantees a good process
The tester follows predefined testing protocols, minimizing deviations and ensuring consistency in the testing process.
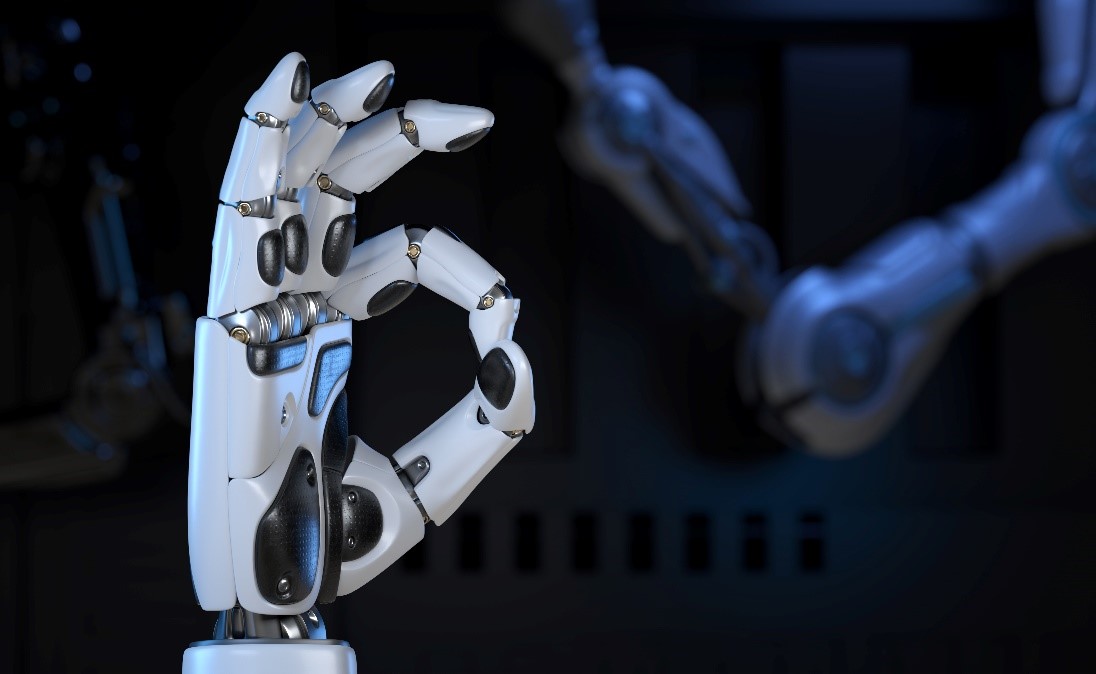
Protects against human error
Human error is inherent in manual testing processes but is significantly reduced with the use of an electrical tester. Automation minimizes the risk of mistakes caused by fatigue, distraction, or oversight.
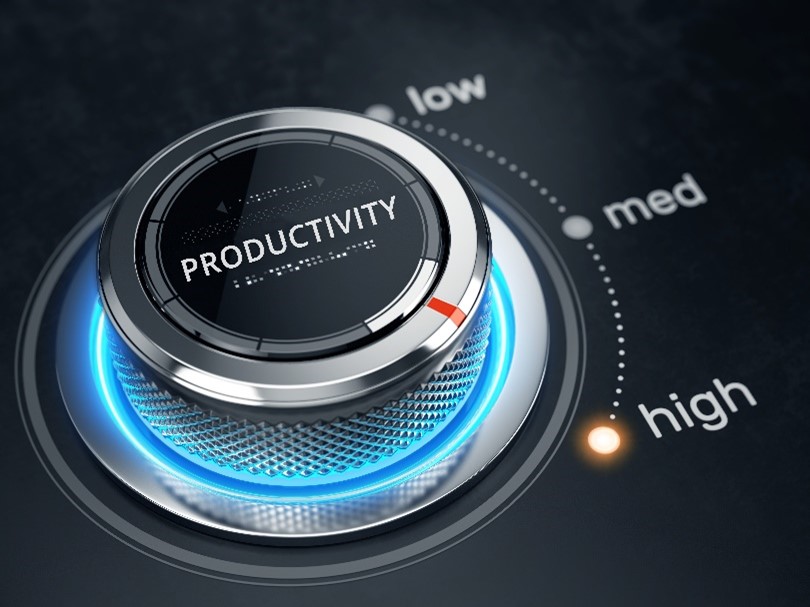
Higher throughput compared to other systems
Automation and optimized testing algorithms enable rapid testing of multiple components within a shorter timeframe, increasing production efficiency and reducing time-to-market.
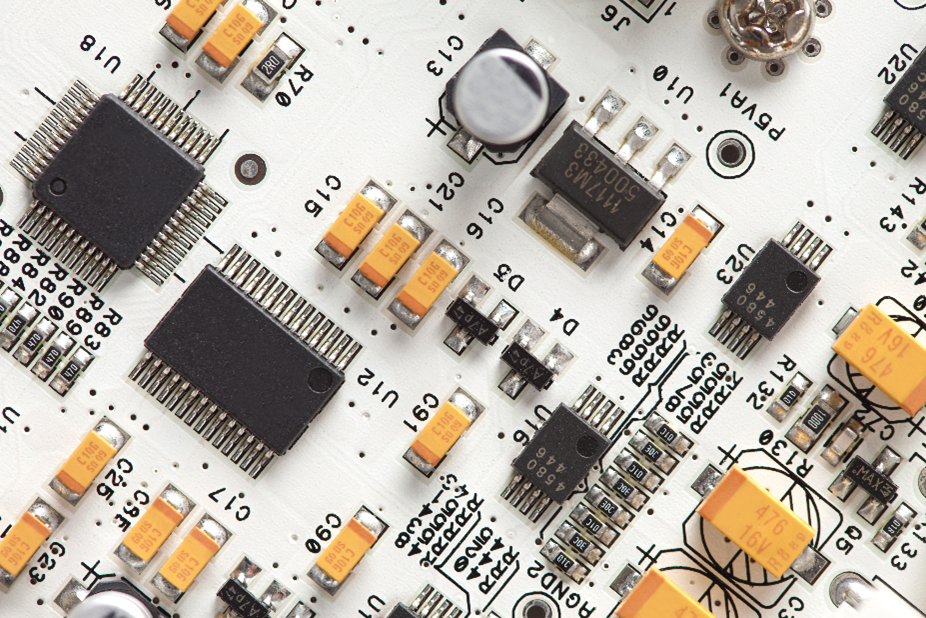
Ability to test small sized packages (down to 01005 dimensions)
The electrical tester ensures that even the smallest electronic components, commonly found in modern electronic devices, undergo rigorous testing for functionality and quality assurance.
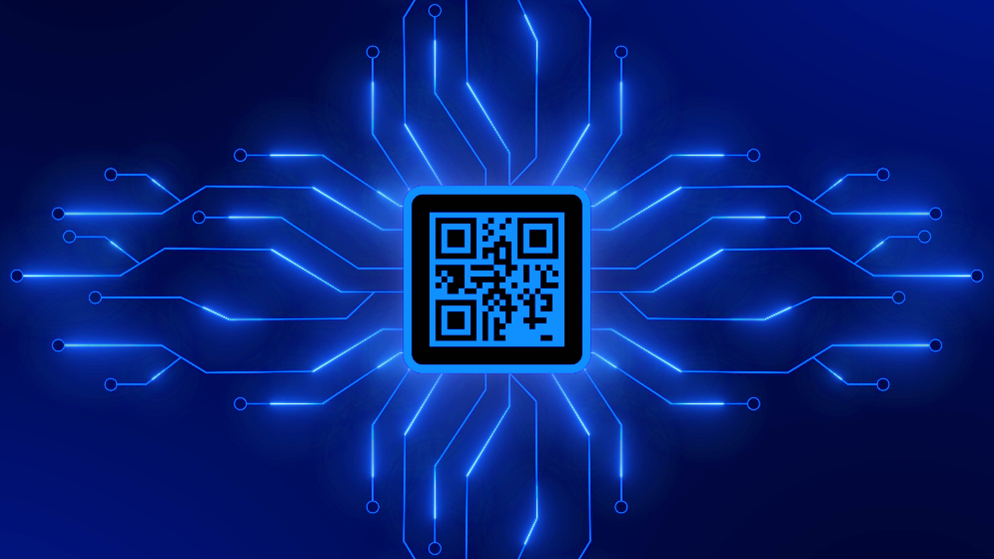
Links with Traceability technology to log all test data for analysis
Traceability improves quality, aids defect analysis, and ensures regulatory compliance, enhancing transparency and accountability in manufacturing.
Technical Data
Electricial Test | |
---|---|
Component dimensions range | from 01005 to 8mm x 12mm |
Resistors | from 0 to 4M Ω |
Capacitors | from 1pF to 300μF |
Inductors | from 2μH to 100H |
Diodes | Up to 36V |