Ensure quality amid complex component challenges
Published: October 26, 2023
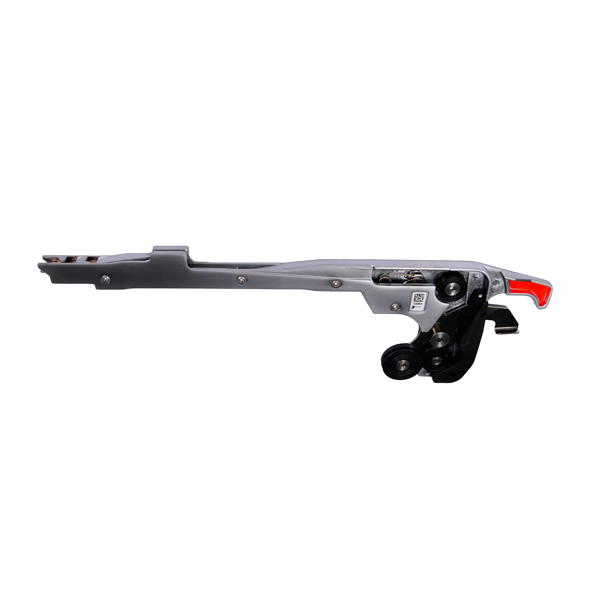
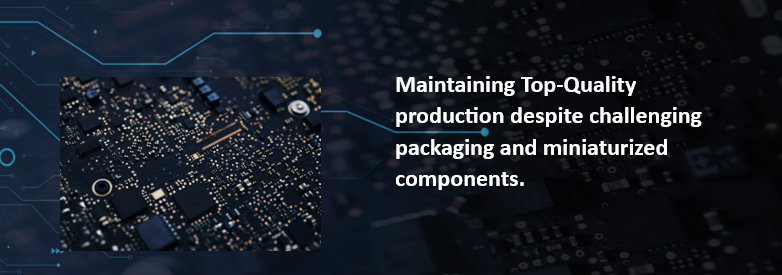
Introduction
In today’s dynamic manufacturing environment, integrating complex and small components into workshops presents a significant challenge. While these miniaturized devices promise innovation and efficiency, they also bring the risk of increased production rejections. In this article, we’ll explore the key factors behind this issue and provide solutions to address it effectively.
High reject rates root causes in production
In the world of component assembly, two factors hold the key to achieving top-quality picks: selecting the right picking tool and configuring the component pick. When it comes to resolving production challenges using methods like the 8D or QRQC, it’s crucial to start by examining these aspects.
Optimizing the suction surface and precisely covering the inner diameter of the nozzle, tailored to the size and tolerance of your components, is one of the critical steps towards successful picks. Moreover, according to component size, steric geometrical factor and head type, a delicate fine-tuning of process parameters should be performed. Addressing these process parameters effectively can significantly reduce pick rejection rates and enhance your production efficiency.
For tiny components, a notable issue arises that pick rejections often result from improper component orientation within the tape’s cavity. To address this challenge and effectively support your production goals, it is essential to identify the key factors and sources of variation causing this problem.
The design of the cavity, in particular the clearance around your components, plays a key role in the success of the picking process. Striking the right balance is essential: the cavity must be spacious enough to avoid stress during picking yet narrow enough to maintain the ideal position and orientation of your components.
A slight clearance is typically acceptable, as long as it remains consistent. In cases where component’s shift behaviour is consistent, our integrated closed-loop vision-picking system is designed to compensate for variations, ensuring your success.
During assembly, uncovering tape covers can sometimes result in the generation of static electricity, impacting component positioning during picking. Additionally, adhesive tape covers can cause components to become stuck or even ejected from their designated cavities during advancement.
Addressing these issues requires careful attention to material properties and the implementation of appropriate measures to minimize static charge and adhesive interactions, all to ensure your production success.
In the world of small, lightweight components, vibrations and varying tape advancement speeds can be challenges that affect component orientation during picking. These factors can introduce unintended variations that may impact your assembly quality.
Europlacer’s new feeding solution for thin components
To empower you in overcoming these challenges, Europlacer introduces the new ii-Feed. This advanced feeder incorporates magnetic elements in the pick-up zone, ensuring secure component positioning and orientation, even in the presence of vibrations and varying tape speeds.
For those seeking further information on the innovative magnetic ii-Feed and its compatibility with various platforms, we encourage you to contact our dedicated customer service team. With the right tools and knowledge, we can collectively navigate the intricate landscape of small component assembly and optimize your production processes.
ii-Feed – Standard
ii-Feed – Magnetic