RC is the software that powers your placement machines and off-line stations
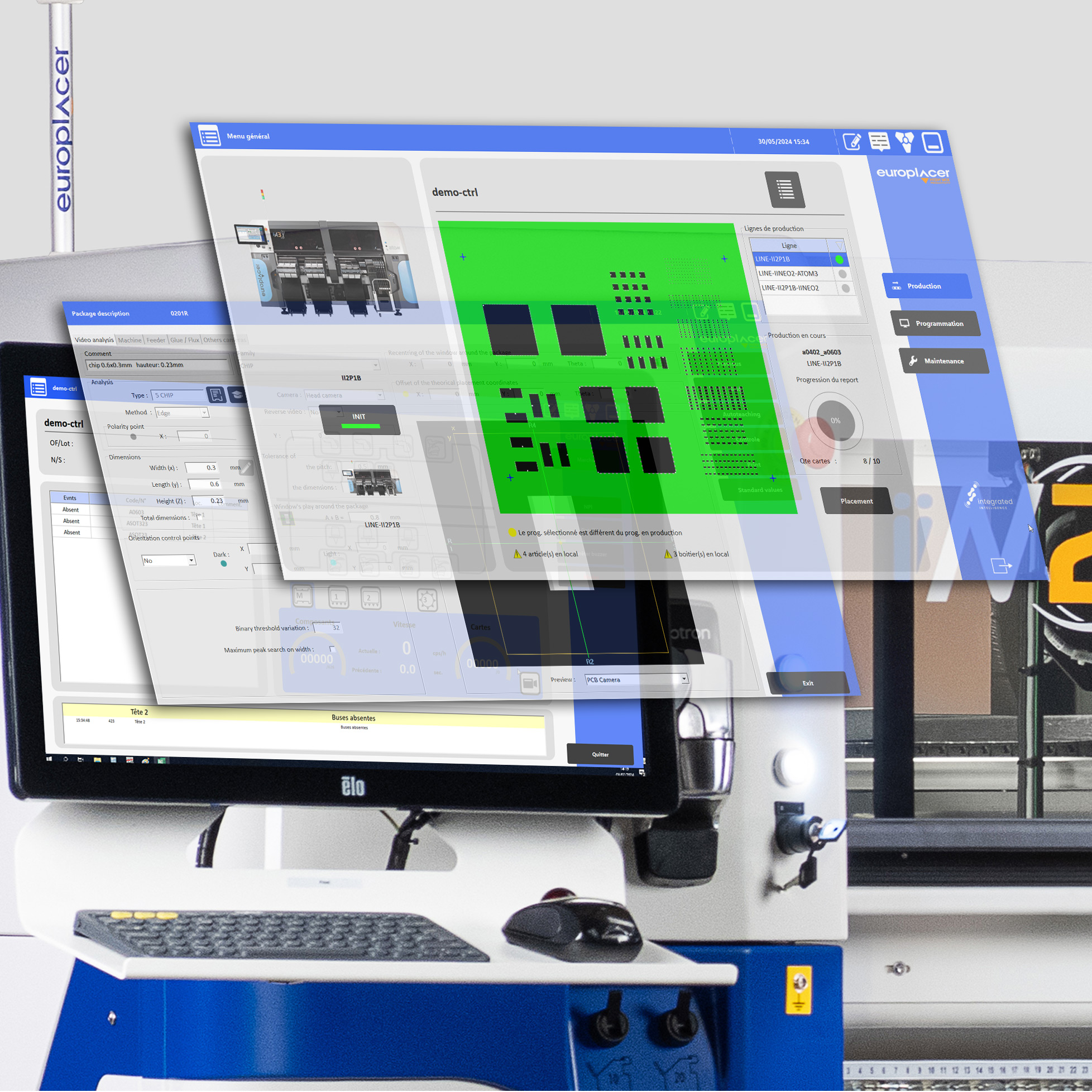
Description
As an integral part of the Europlacer software solutions ecosystem, ii-RC supports you at every stage of your SMT assembly process. ii-RC is not only the interface that allows you to interact with your placement machines, it’s the heart of functionality on dedicated workstations: to ensure the preparation of your feeders, to manage your component stock, to generate your placement programs and optimize them, or even to undertake the recognition process to learn your electronic components. And much more!
Every workstation and machine using ii-RC software communicates seamlessly to deliver an interconnected environment and expedite procedures while eliminating unnecessary data manipulation. Thanks to our policy of backwards compatibility, you can benefit from the latest versions of ii-RC software and enjoy its advantages even on your oldest Europlacer machines.
Features / Benefits
In its latest version, RC5-17 software incorporates new features that revolutionize the way you work.
Here are a few examples:
- ii-RC has a new look and feel, with a more ergonomic interface and a much-improved user experience, particularly through touch-screen management.
- As standard, it integrates the management of Gerber layers during the definition of your programs. Thanks to this functionality, it frees you from using valuable machine resources, allowing you to prepare your future production entirely off-line.
- Data logging to give total traceability of modifications to your parameters and to machine libraries. It provides maximum control over your quality standards.
- Verification and calculation tools that eliminate any human or component stock assessment errors.
- Multi-line optimization that will allow you to switch a production program from one line to another without having to worry about re-optimizing.
- A wizard to create electrical test procedures for your components. The definition of stringent electrical test procedures which is usually reserved for expert teams.
- MariaDB standardized database, to easily extract data via SQL requests.
- High-Resolution Treatment: Can manage smaller components (down to 03015m) and finer pitch (down to 0.15mm for µBGA with optional fixed camera).
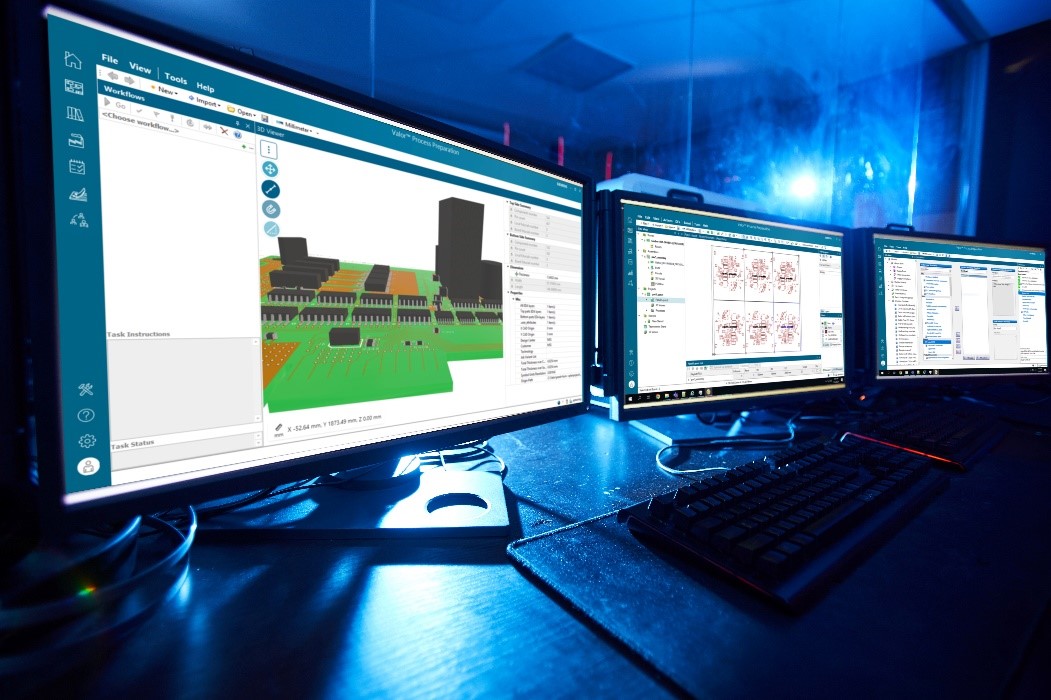
Siemens Process Preparation X
Siemens Process Preparation X’s ability to import different types of CAD files and expand the core library to 6,000 components (from the standard 400) streamlines the design process. This reduces the manual work involved in creating components and speeds up design iterations, which ultimately translates into a shorter time-to-market.
With an additional possible access to over 300 million packages and direct links to Manufacturer Part Numbers (MPNs) and manufacturers as an option, Siemens Process Preparation X allows you to verify component selection and sourcing. This integration ensures the accuracy and availability of component information. In addition, Siemens Process Preparation X’s rigorous validation of BOMs and AVLs minimizes the risk of errors, ensuring compliance with quality standards and improving product reliability.
Siemens Process Preparation X software simplifies the screen-printing process by making it easier to design stencils and ensures consistency and regularity throughout. With its advanced capabilities, it accurately matches PCB layouts, ensuring precise solder paste deposition critical for achieving top-tier solder joints.
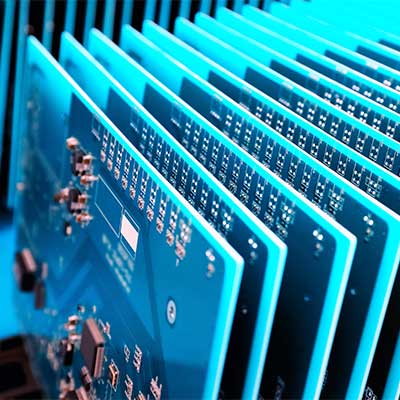
Stock Management
Europlacer’s “Stock Management” option enables traceability for all components in storage or on the shop floor. It gives users the ability to easily locate all components and discover the remaining quantities in real time, while production is still running.
When combined with our storage systems, component management becomes a fully controlled & integrated process for a true Industry 4.0 experience.
The Stock Management station is controlled by our ii-Tab for the programming of Europlacer’s intelligent feeders. Key benefits include the ability to track the quantity on each individual reel, whether connected on the machine, feeder storage, or in stock.

Set-up Help
Set-up help facilitates the new product introduction from a programming station by preparing the machine loading for the next job without interrupting production.
Europlacer’s placement machines utilise unique, truly intelligent feeder technology. The machine or the offline programming station communicates with the intelligent feeders. All feeders are fitted with LED indicators that will be used to inform the operator about feeders required for the next batch.
After selecting the next job ‘B’, the required items are automatically searched for on the machine and on any external storage zones which are connected. Feeders that are connected, either on machines or on the storage racks and trolleys, can be highlighted for processing.
Components not loaded are listed so that feeders can be prepared while job ‘A’ is still running.
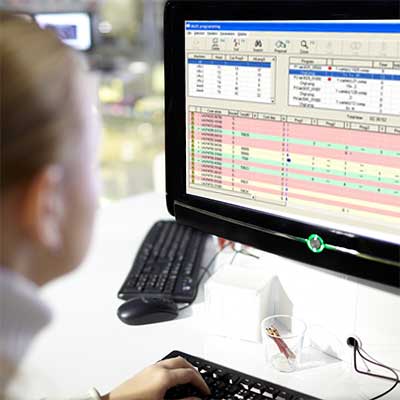
Multi-job Optimiser
Our Multi-job optimiser option creates common loading plans for groups of jobs, it minimises feeder changes, significantly reduces product changeover times and improves the general throughput of the line.
The optimiser is a simple graphical tool to improve the efficiency and throughput across a single machine or a series of multiple machine lines.
Being able to review and plan workload and loading patterns in advance, whilst reacting to component shortages or re-priorities in real time is an important factor in a high mix environment.
Further optimisation of the manufacturing efficiency can be achieved using multi-programming software to produce the optimum production schedule for manufacture.
A GUI-driven software system shows an image of each board/job and enables the operator to:
- Choose jobs
- Choose the machine or line.
The system then optimises the jobs based on throughput and changeover time, providing an accurate time readout that can be used in job quotations.
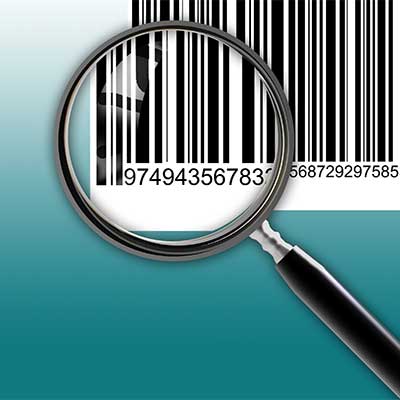
Total Traceability
Being able to determine ‘what happened and why?’ is an important ability, especially within a fast and dynamic production environment.
Traceability provides a full and expandable solution as it is able to monitor and record not only the component source, but the full process the component was subjected to, including feeder type and serial number, test processes and results – and ultimately the fully assembled PCB detail.
Total Traceability lets users integrate full traceability into the production process. This intelligent system provides full data logging for component-level build traceability. It generates data for each board produced. The PCB camera reads board codes while the intelligent feeders hold batch data. The archive can be processed by PROMON production monitoring software or exported for traceability analysis. Based on product identifi cation, the system also permits automatic program loading to streamline changeover.
We record all the data automatically and can integrate with external sources for trend analysis and data collection.
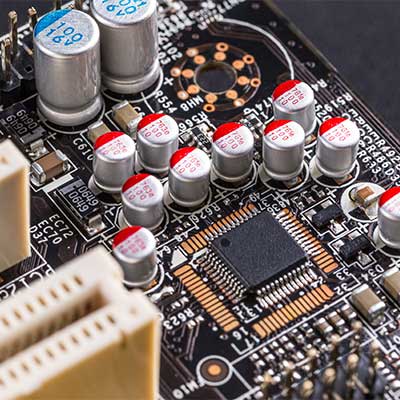
Auto Adaptive Sequencing
A.A.S is a unique and powerful Europlacer tool which eliminates, in real time, potential placement issues caused by poor programming or component run-out in production.
A.A.S automatically defines placement priorities depending on the components already placed, to create a collision-free placement sequence. The process starts with program generation where getting the placement program right first time results in an improved process and a better quality product.
This complex task is fully automatic and considers the placement sequence around parameters including component package, PCB topology, head trajectory and the optimal placement sequence.
On densely populated boards, there is potential for nozzles to influence a previously placed component. A.A.S gets all component data from the library (physical dimension, nozzle type, placement parameters etc.) and then analyses the possible placement scenario to create placement rules for each component.
These rules are applied automatically and are constantly monitored during a full production run guaranteeing optimal performance and quality of product.
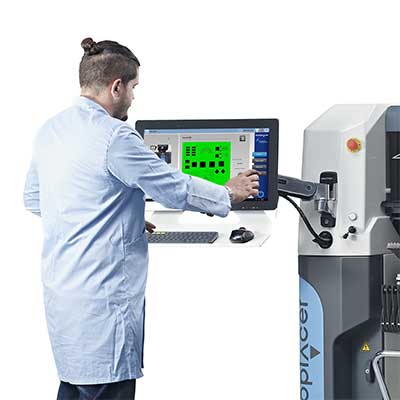
NPI
NPI is a fundamental process for any operation that requires a fast and seamless new product introduction process.
Used to validate any new product ahead of being processed, NPI gives the user complete control of package and programming details without interfering with live production, keeping throughput efficiencies high.
Being able to load a CAD or Gerber file and validate component type, orientation, feeder type etc. ahead of production before placing any component.
After loading a new PCB in the machine, operators just need to follow the different steps that help to check and validate all parameters involved in the new product. When an error is detected, the software allows the operator to make corrections and test without halting production.
Fiducial marks, placement coordinates and orientation of the components (an overlay is placed on top of the image), nozzles, feeder set-up and feeder controls will be validated. The operator has the possibility to temporarily delete some items, patterns and references . The production can then start safely without any further adjustment.