RC est le logiciel qui alimente vos machines de placement et vos stations hors ligne
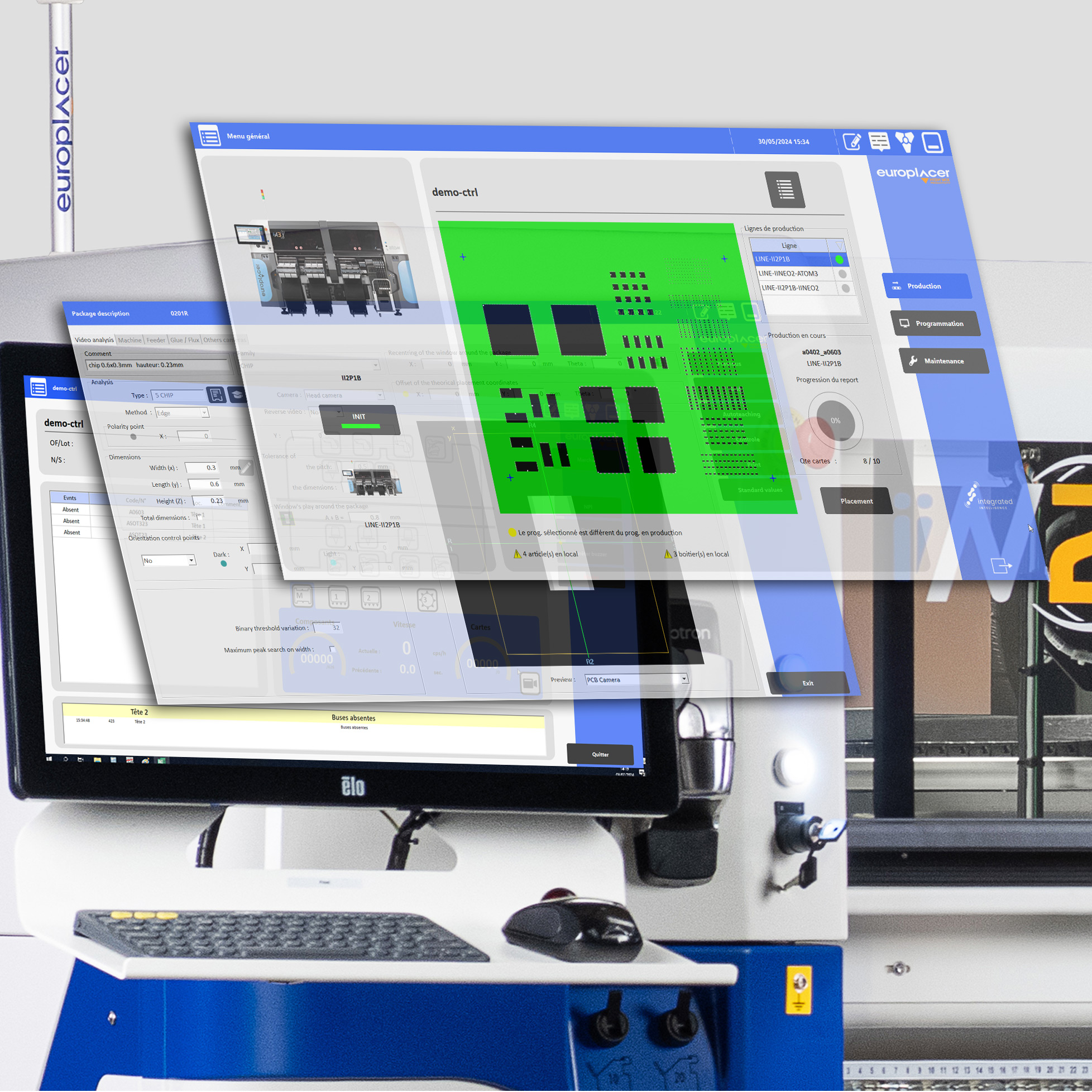
Description
Cœur de l’écosystème des solutions logicielles Europlacer, ii-RC vous accompagne à chaque étape de votre process d’assemblage CMS.
ii-RC est non seulement l’interface qui vous permet d’interagir avec vos machines de pose, mais aussi avec les postes dédiés tels que: la préparation des chargeurs, la programmation et l’optimisation du placement ainsi que la réalisation des algorithmes des composants spécifiques et plus encore.
Chaque poste et machine utilisant le logiciel ii-RC communique pour vous garantir un environnement interconnecté et gagner en rapidité tout en éliminant les manipulations de données superflues. Grâce à notre politique de rétrocompatibilité, vous pouvez profiter des dernières versions du logiciel ii-RC et de ses bénéfices même sur vos plus anciennes machines de placement.
Caractéristiques / Avantages
Dans sa dernière version, le logiciel RC5-17 intègre des nouvelles fonctionnalités qui révolutionnent votre manière de travailler. ii-RC fait peau neuve en accentuant l’ergonomie de son interface et en améliorant nettement l’expérience d’utilisation notamment par la gestion de l’écran tactile.
En voici quelques exemples:
- Intégration de série la gestion des couches Gerber lors de la définition de vos programmes. Grâce à cette fonctionnalité, vous vous affranchirez d’utiliser des ressources machines et préparez vos futures productions totalement hors-ligne.
- Intégration de la journalisation en offrant une traçabilité totale sur la modification de vos paramètres et librairies machines. Ainsi, vous vous garantissez un contrôle optimal de vos standards de qualité.
- Disponibilité d’outils de vérification et de calcul qui éliminent toute erreur humaine d’évaluation des stocks.
- Optimisation multi-lignes qui vous permettra de passer un programme de production d’une ligne à l’autre sans avoir à vous soucier de la ré-optimisation.
- Une assistance numérique pour créer des procédures de test électrique pour vos composants, habituellement réservées à des équipes d’experts.
- Une base de données standardisée MariaDB, permettant d’extraire facilement des données via des requêtes SQL.
- Un traitement d’image à très haute résolution : capable de gérer avec un caméra fixe optionnelle, des composants plus petits (jusqu’à 03015) et des pas plus fins (jusqu’à 0,15 mm pour les µBGA).
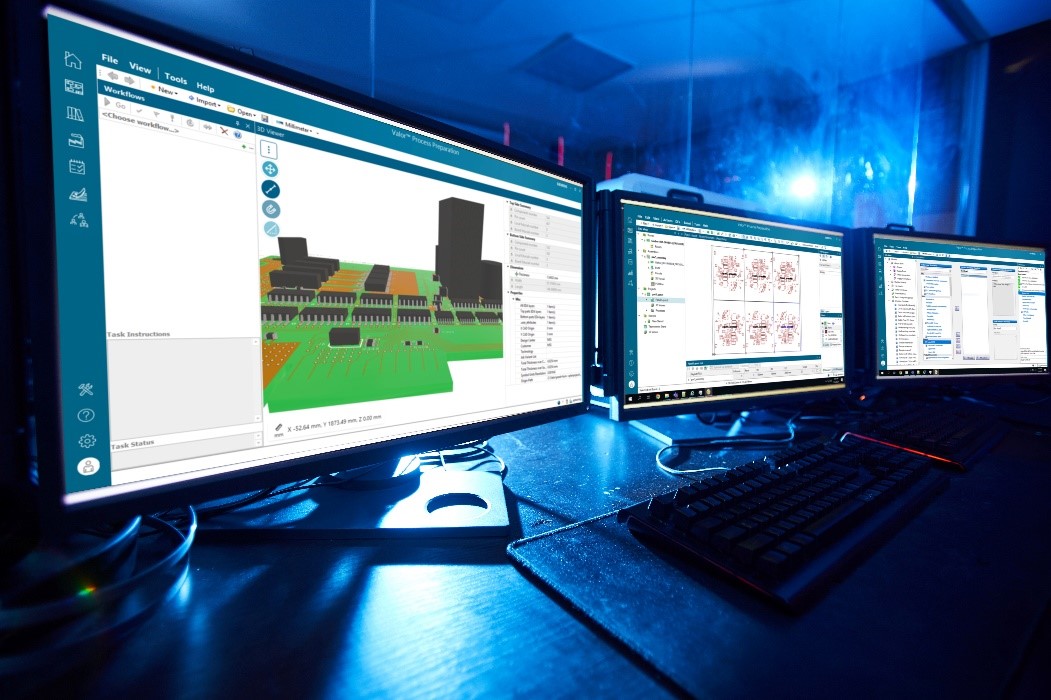
Siemens Process Preparation X
La capacité de Siemens Process Preparation X à importer différents types de fichiers CAO et à étendre la bibliothèque de base à 6 000 composants contre 400 en standard, rationalise le processus de réalisation des programmes de pose. Cela réduit le temps de saisie manuelle nécessaire à la création des boitiers en accélérant et rationalisant les étapes.
Avec en option un accès possible à plus de 300 millions de composants et des liens directs vers les part number des fabricants (MPN) et de leurs bases des données, Siemens Process Preparation X facilite la vérification et l’approvisionnement des composants. Cette intégration garantit l’exactitude et la disponibilité des informations sur les composants et la validation rigoureuse des nomenclatures et des listes de fournisseurs approuvés (AVL) par Siemens Process Preparation X.
Siemens Process Preparation X simplifie le process de sérigraphie en facilitant la conception des pochoirs et en assurant cohérence et régularité de l’ensemble. Grâce à ses fonctionnalités dédiées à la sérigraphie, Siemens Process Preparation X garantit une précision optimale dans le respect du design de l’écran de sérigraphie. De cette précision maximum dépend la qualité de dépôt de la crème à braser et de la qualité des joints soudés.
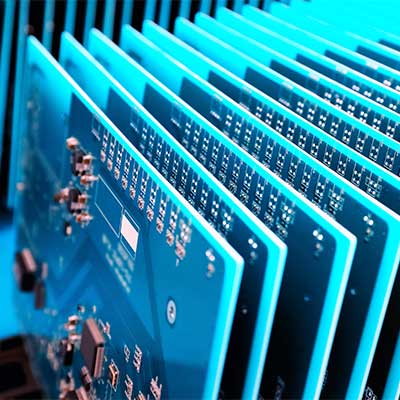
Gestion des Stocks
La gestion de stock offre aux utilisateurs la possibilité de localiser facilement tous les composants et de connaître les quantités restantes en temps réel, alors que la production est toujours en cours. Combinée à nos systèmes de stockage, la gestion des composants devient un processus entièrement contrôlé, intégré et fluide.
La station de gestion des stocks est contrôlée par ii-Tab, permettant la programmation des chargeurs intelligents d’Europlacer. Les avantages clés incluent la possibilité de suivre la quantité sur chaque bobine individuelle, indépendamment du fait que celle-ci soit connectée à la machine, à une étagère de stockage de chargeurs ou au stock.

Assistance à la Préparation
L’assistance à la préparation facilite l’introduction d’un nouveau produit à partir d’une station de programmation en préparant le chargement de la machine pour le programme suivant sans interrompre la production.
Les machines de placement Europlacer utilisent une technologie de chargeurs unique et véritablement intelligente. La machine ou la station de programmation hors ligne communique avec les chargeurs intelligents. Tous les chargeurs sont équipés d’indicateurs à LED qui seront utilisés pour informer l’opérateur de ceux nécessaires à la production du prochain lot de cartes.
Après la sélection du programme suivant « B », les articles requis sont automatiquement recherchés sur les machines et sur les zones de stockage externes connectées. Les chargeurs connectés, que ce soit sur machines, étagères ou chariots de stockage, peuvent être mis en évidence pour traitement.
Les composants non chargés sont répertoriés afin que les chargeurs puissent être préparés pendant que le programme « A » est en cours de production.
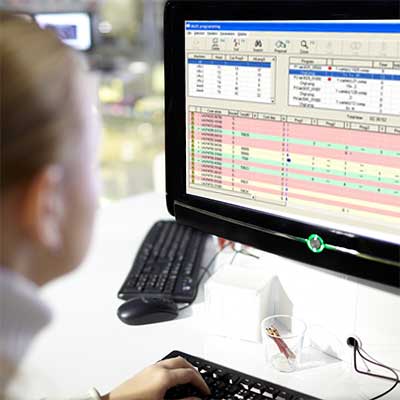
Optimiseur multi-programmes
Notre option d’optimisation multi-programmes crée des plans de chargement communs pour des groupes de programmes. L’optimiseur minimise les changements de chargeur, réduit considérablement les temps de changement de production et améliore le débit général de la ligne.
L’optimiseur multi-programmes est un outil graphique simple destiné à améliorer l’efficacité et la cadence sur une seule machine ou une série de plusieurs machines en ligne.
Pouvoir analyser et planifier la charge de travail et les plans de chargement à l’avance, tout en réagissant en temps réel aux pénuries de composants ou à la redéfinition des priorités, est un facteur important dans un environnement où la mixité est élevée.
Il est possible d’optimiser davantage l’efficacité de la fabrication en utilisant un logiciel d’optimisation multi-produits afin de créer un programme de production optimal.
Un système logiciel piloté par une interface graphique affiche une image de chaque carte/programme et permet à l’opérateur de :
- Choisir le programme à effectuer
- Choisir la machine ou la ligne à utiliser pour la production.
Le système optimise ensuite les programmes en fonction de la cadence et des temps de changement, en fournissant des données précises de temps de production très utiles pour établir les offres commerciales.
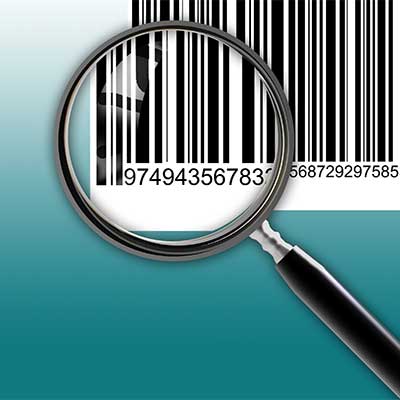
Traçabilité Totale
Être capable de déterminer « qu’est-il arrivé et pourquoi ? » est une fonctionnalité déterminante pour répondre aux exigences imposées par vos clients et assureurs.
La traçabilité Europlacer fournit une solution complète et évolutive, capable de surveiller et d’enregistrer non seulement la source du composant, mais également le processus complet auquel le composant a été soumis, y compris le type de chargeur et son numéro de série, les processus de test et les résultats, ainsi que le détail du circuit imprimé entièrement assemblé.
La Traçabilité totale permet aux utilisateurs d’intégrer une traçabilité complète dans le processus de fabrication. Ce système intelligent fournit un enregistrement complet des données pour une traçabilité de la production au niveau des composants. Il génère des données pour chaque circuit produit. La caméra carte lit les codes des cartes et les chargeurs intelligents contiennent les données du lot. Les archives peuvent être traitées par le logiciel de surveillance de la production PROMON ou exportées pour une analyse de traçabilité. Sur la base de l’identification du produit, le système permet également le chargement automatique du programme afin de simplifier les changements de production.
Nous enregistrons toutes les données automatiquement et pouvons intégrer des sources externes pour l’analyse des tendances et la collecte de données.
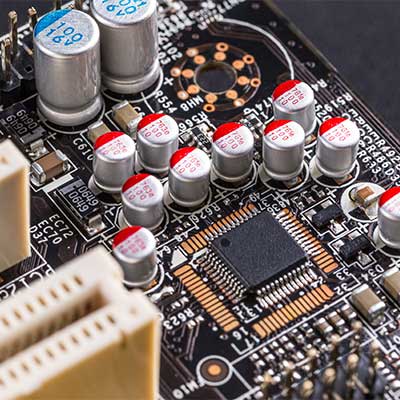
Séquençage Auto-Adaptatif
Le séquençage auto-adaptatif (A.A.S.) est un outil Europlacer, unique et puissant, qui élimine, en temps réel, les problèmes de placement potentiels causés par une programmation médiocre ou le manque de composants en production.
Le séquençage auto-adaptatif définit automatiquement les priorités de placement en fonction des composants déjà placés, afin de créer une séquence de placement sans collision. Le processus commence dès la création du programme, dans le but d’obtenir un programme de placement correct dès la première carte, afin d’assurer un process correct et un produit de meilleure qualité.
Cette tâche complexe est entièrement automatisée et prend en compte la séquence de placement autour de paramètres tels que l’encombrement des composants, la topologie du circuit imprimé, la trajectoire de la tête et la séquence de placement optimale.
Sur les cartes densément peuplées, les buses peuvent potentiellement influencer un composant précédemment placé. Le séquençage auto-adaptatif extrait toutes les données du composant à partir de la bibliothèque (dimension physique, type de buse, paramètres de placement, etc.), puis analyse les scenarios de placement possible afin de créer des règles de placement pour chaque composant.
Ces règles sont appliquées automatiquement et font l’objet d’une surveillance constante pendant toute la production, garantissant des performances et une qualité de produit optimales.
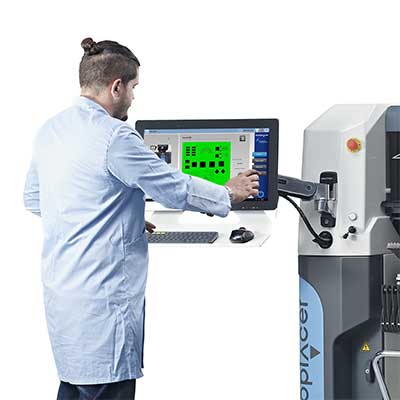
NPI
L’introduction d’un nouveau produit (NPI) est un processus fondamental pour un lancement de production rapide et efficace.
Utilisé pour valider tout nouveau produit avant son lancement en production, le NPI permet à l’utilisateur une vérification globale des boitiers et de la programmation sans interférer avec la production en cours, permettant ainsi de maintenir des rendements élevés.
Capable de charger un fichier CAO ou Gerber, il permet de valider le type de composant, son orientation, le type de chargeurs, etc. en amont de la production, avant même de placer un seul composant.
Après avoir chargé un nouveau circuit imprimé dans la machine, il suffit aux opérateurs de suivre les différentes étapes permettant de vérifier et de valider tous les paramètres impliqués dans le nouveau produit. Lorsqu’une erreur est détectée, le logiciel permet à l’opérateur de faire des corrections et d’effectuer des tests, sans avoir à interrompre la production.
Les marques de recalage, les coordonnées de placement et l’orientation des composants (un dessin du contour est mis en surimposition sur l’image), les buses, la configuration et les commandes du chargeur seront validés. L’opérateur a la possibilité de supprimer temporairement certains articles, motifs et références. La production peut alors démarrer en toute sécurité sans autre ajustement.